ハヤカワ電線工業株式会社 様
OCRハンディターミナルで基幹と連携
高い検品精度で入荷即出荷の体制を支える
ワイヤーハーネスの製造・販売会社
兵庫県姫路市に本社を置くハヤカワ電線工業株式会社を代表とするハヤカワグループ様は、車載、家電製品、産業機器、OA機器、ガス機器や医療機器などの電気製品に電気を供給するワイヤーハーネスの製造・販売を行っています。国内約200社のメーカーから電線や端子等の製品パーツを仕入れ、在庫することなく即出荷の体制で、海外に展開する18カ所の自社組立工場に、航空便と船便で輸出しています。処理件数は月1万8千件、アイテム数は2万件に上ります。
仕入製品の入荷・検品・出荷を担う物流センターは3か所、うち姫路市内にある姫路・林田の2カ所のセンターに2020年11月「検品支援名人」が導入され効果を上げています。
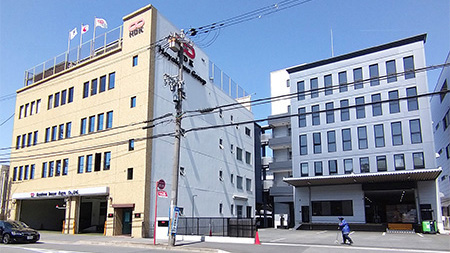
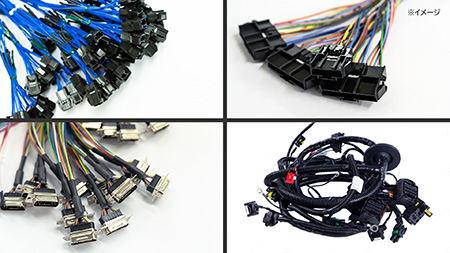
すべてにアナログな物流業務、その簡素化と見直し
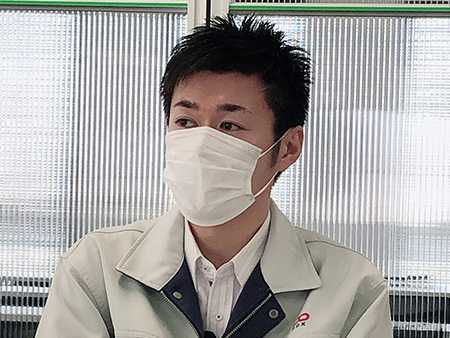
同社経営管理本部・総務グループの本勝サブリーダーは、
「第一に、すべてにおいてアナログな物流業務を行っていた運用プロセスが問題でした。紙ベースと手入力によりヒューマンエラーがいずれ起こるだろうと思っていましたし、実際数件起こっていました。
第二に、プロセスの簡素化と見直しが必要でした。ベテランのスタッフが居ないとうまく回らない。それは、やはりプロセスの簡素化ができていなかったのが問題。」と、導入の背景となった要因を説明いただきました。
導入前の業務の流れ
梱包の中身と添付された納品書内容の照合。その伝票を持って事務所との往復。入・出荷とは別の場所で行われる基幹システムへの手入力。
スタッフの目と経験に頼り、紙のアナログベースで行っていた業務には、手間とミスのリスクが常に付きまとっていました。
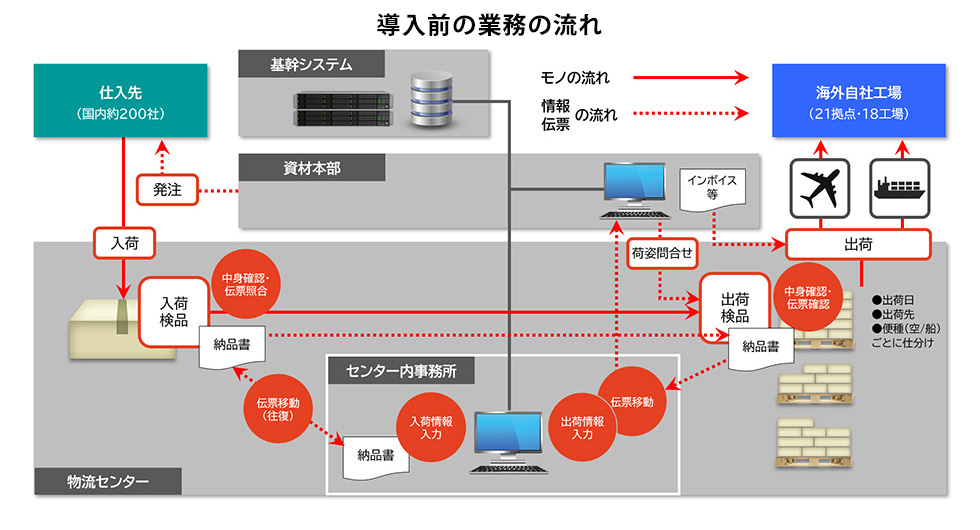
検品システムの検討と3つの選定ポイント
そこで、同社では業務のシステム化を検討。3社による提案のなかで「検品支援名人」が選ばれました。選定の理由として、本勝サブリーダーは「3社のなかで、群を抜いてユーザックシステムの提案が良かった。」として、以下の3点を挙げます。
1.基幹システムとの連携
基幹システムは自社独自のシステムを構築しており、「検品支援名人」であれば問題なく連携できること。
2.サポート力
何かの時にでも即対応してもらえる体制が整っていること。
3.今後の拡張性
さまざまなシステムを今後組み込み、物流システムの統合化を図る計画で、それらともスムーズに連携が図れること。
導入後の業務の流れ
キーエンス社製のハンディターミナルで、納品書にある英数字の注文番号をOCR機能により読み取り、基幹システムに照会し入荷検品処理を行います。また、ラベルプリンタで専用のQRラベルを出力し、出荷管理に活用するなど、情報の一元化によりスムーズで高い精度の業務を実現しています。
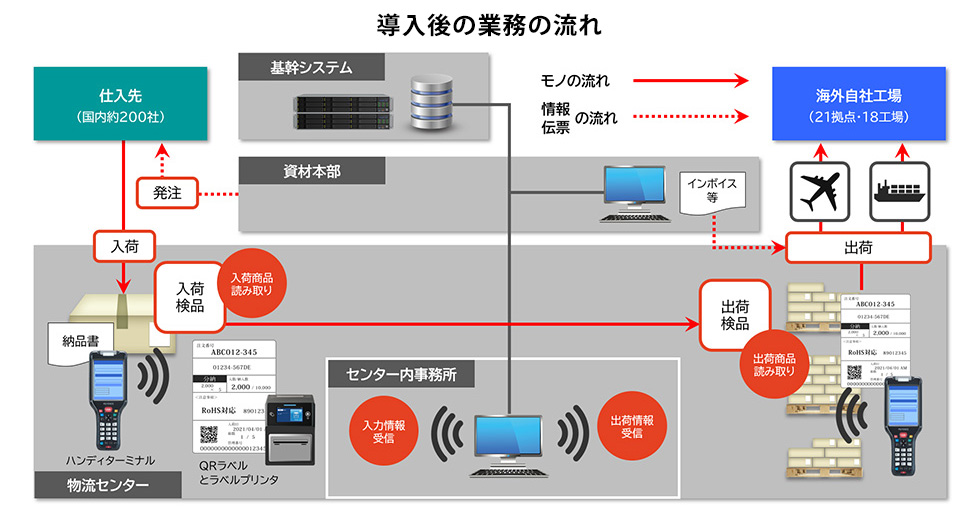
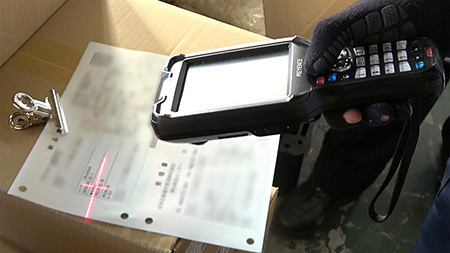
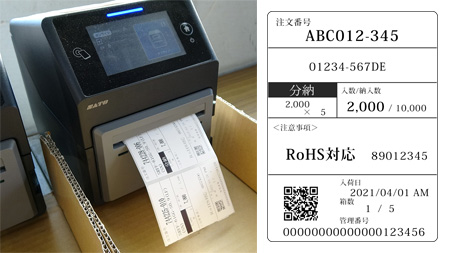
パレット番号の割り振りと、ハンディターミナルへの不安の払しょくに苦労
苦労した点について、本勝サブリーダーは、
「自社海外工場が20数拠点あり、注文番号によって出荷パレットの番号が変わってくるので、納入先の番号をどう割り振っていくかが悩ましいところでした。また、商品を検品後、入荷時の箱のまま出荷するのが基本だが、場合により混載する梱包も発生するのでそれらをどう登録すればいいか、システムと現場とのすり合わせに試行錯誤を重ねました。
さらに、大半のスタッフはハンディターミナルを扱った経験がなく、「私の仕事が無くなってしまうのでは」という不安を取り除くのも大変だった。」と振り返ります。
導入の効果、体力面・精神面にも
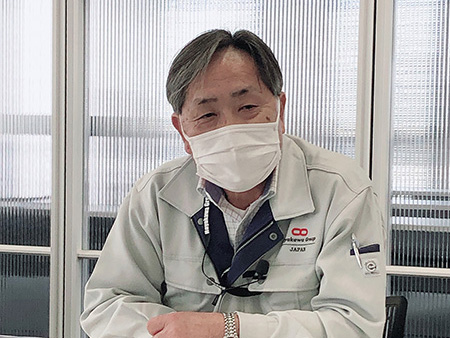
システム導入の効果について、内海取締役にお話しいただきました。
「スタッフ数は、姫路・林田の物流センター合わせ、導入前20名が15名に5名減員することができました。(定年退職等の自然減で対応)
勤務時間では、以前は夜8時、9時におよぶことも頻繁にありましたが、最近では30分~1時間程度の延長に抑えられており、体力的には楽になっているのではと思います。
これまでは、「人間の目」「人間の手」に頼る作業であったためエラーや間違いが多々発生していました。今回のシステムの一番の特徴は、それらを極力避け、OCRの「機械の目」で取り込んだデータをそのまま基幹システムと連携して運用するため、精神的な負担が軽減し作業効率が向上したこともシステム導入の効果としては大きい。第1段階としての導入はほぼ成功。」とのことです。
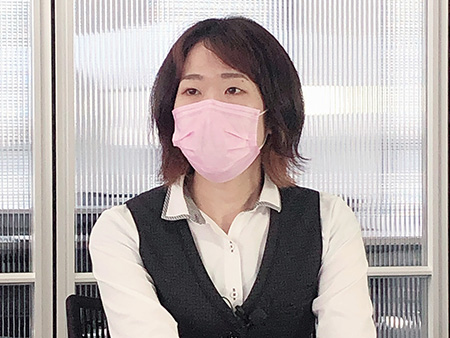
物流センターと密接に連携し、購買・調達・輸出業務を担う資材本部の内海サブリーダーにも評価をうかがいました。
「資材としては、物流センター側での出荷処理が終わってからでの業務となるので、これまでは夜遅くまで待つこともしばしばでした。輸出書類の提出も時間が決められているので、資材から応援を行うこともありましたが、今はそういったことがなくなりました。
また、荷姿が私たちからは判らないので、逐一現場に梱包の状態を確認し、回答を待ってから輸出の手続きを進めていたのですが、導入後はシステム上で確認することができるので、資材側でもメリットが大きい。」
現場では
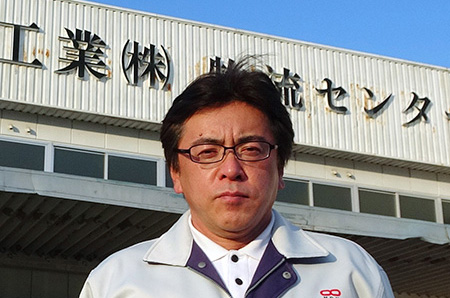
現場の様子を、同社最大の物流拠点である林田物流センターの山本センター長に尋ねました。
「システム構築にあたっては、従来の動きをもとに、業務の流れをあまり変えないようにつくってもらった。QRラベルの貼り間違いさえしなければ出荷のエラーは起こらない。システムにより、うっかりミスは防げるので、その点はいいと思う。なぜ導入を決めたかというと、『何かの第一歩』になるんじゃないかと思って進めたところもある。」との含みのある言葉でした。
その『第一歩』とは? 最後に「検品支援名人」導入を機に計画されている将来構想をうかがいました。
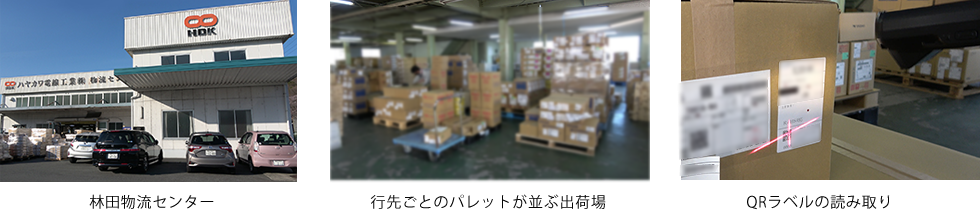
「検品支援名人」を緒とする将来構想、システム・拠点の両面で
システム面での構想について、本勝サブリーダーは、
「次のステップとしては、自動採寸・計量機を導入し、3点計測等の計量自動化により、資材本部が担当するインボイスやパッキングリストへの連動を図りたい。さらに、現在仕入先と行っているWeb-EDIと当システムとの連携を実現させたいと考えています。これらにより、物流システム(検品名人・自動計測)・Web-EDI・基幹システムの3者で、データを連携させることで、大幅な業務効率化をめざしています。
一方、物流拠点の構想に関して、内海取締役は、
「林田・姫路・製品(海外工場から輸入した完成品を国内販売)物流部門の3部門で展開している物流業務を、近い将来は1カ所で集中的に作業ができる体制に整えたい。また、今回のシステムは、マテハン・自動倉庫ライン構築の流れの一歩にもあたります。大規模な投資にはなるが、4~5年内には、統合物流センターの構築を計画しています。今回は『点』でのシステム化だが、将来的には一つに集約化していきたい。その際にはまたユーザックシステムさんにもお手伝いいただければ。」
とのことでした。
「検品支援名人」の導入により、
1.従来の業務プロセスを見直し、業務の効率や精度を向上させたこと。
2.その手法として、人の目や手をサポートするハンディターミナルを導入し、基幹システムと連携させたこと。
3.今回のシステムが、将来の物流拠点の統合やシステム連携を見据えた第一歩となること。
など、さまざまな効果を発揮するとともに、その役割はますます大きく重要になっていくものと期待されています。